ohio gen alternator for 2007 pathfinder
Printed From: the12volt.com
Forum Name: Car Audio
Forum Discription: Car Stereos, Amplifiers, Crossovers, Processors, Speakers, Subwoofers, etc.
URL: https://www.the12volt.com/installbay/forum_posts.asp?tid=132251
Printed Date: May 23, 2024 at 9:23 AM
Topic: ohio gen alternator for 2007 pathfinder
Posted By: krush
Subject: ohio gen alternator for 2007 pathfinder
Date Posted: September 24, 2012 at 10:07 AM
Doing the the BIG 3 upgrade for a 2007 Nissan Pathfinder V6 LE. I just placed my order from Ohio Gen for a 300amp monster with 100 to 125 Amps output at 1000RPM. Will put up the spec chart. Any advise would be greatly appreciated. This is my first Alt upgrade on a Nissan.
I was reading up and found out there is a ground-sensor relay on the side of the battery from the neg wire on the battery to the engine and that all the ground must go thru this sensor. So all ground point with have to be from the battery terminal? I will put up pic of the Ohio beast in a few days. Also for power/ground wires, does anyone have recommendations, I was was thing to go with Knukonceptz 1/0 AWG and 4 AWG all the way around.
------------- The best tool in my work shop, is my BRAIN!!!!
Replies:
Posted By: soundnsecurity
Date Posted: September 24, 2012 at 11:38 AM
if the ground has to go through the sensor then dont replace the factory ground, just add a 0 gauge ground to the frame and leave the factory ground alone. this is what i did in my 2011 frontier which is basically the same thing as your pathfinder, also ran knukonceptz 0g in mine too. i havent upgraded my alternator yet but i havent had a reason yet because the factory system keeps up with 1800 watt amp
-------------
Posted By: krush
Date Posted: September 24, 2012 at 12:32 PM
THX for the info soundnsecurity.... its a crime to see the cheap doodie wire Nissan used on the ground. I know a 4awg will fit thru it, but after i remove the factory wire i will have a better idea. Looking at the factory wire it just seam to go thru the sensor and not connecting it in any way?
Ground-sensor on 2007 Pathfinder
My thinking was to replace it with a min of good quality 4awg or better and soldiered terminals. Also remove the paint under the bolt where the ground sensor is bolted down with a smaller 10awg ground wire going to the somewhere under the fuse box ( cause Nissan did the smart thing by grounding on top of the paint  )
Where did you run the frame wire, to the engine ground or to the battery neg? Also did you have to run your amp ground from the neg battery term to the Amp? ------------- The best tool in my work shop, is my BRAIN!!!!
Posted By: soundnsecurity
Date Posted: September 24, 2012 at 10:00 PM
i grounded it to the frame right below the battery, nothing special except that i sanded down to bare metal and then i re-coated it with undercoating after i made the connections. i did not have to run the amp straight to the battery, if you did that then it would make no sense to upgrade the factory battery ground. i just made a solid connection close to the seatbelt bolt on the drivers side.
-------------
Posted By: krush
Date Posted: September 25, 2012 at 9:48 AM
received my XS bus terminals and knukonceptz battery pos and neg mounts yesterday. This will allow me to add the room i need for the added wires and leave the factory connection in-tacked.
Anyone have recommendation for a battery.... I was thinking yellow top? ------------- The best tool in my work shop, is my BRAIN!!!!
Posted By: krush
Date Posted: September 27, 2012 at 11:46 AM
Okay here is what I have found out about Nissan's:
Variable voltage control system:
CAUTION:
- Do not ground accessories directly to the battery terminal. Doing so will bypass the variable voltage control system and the vehicle battery may not charge completely.
- Use electrical accessories with the engine running to avoid discharging the vehicle battery.
Your vehicle is equipped with a variable voltage control system. This system measures the amount of electrical discharge from the battery and controls voltage generated by the generator.
The current sensor (A) is located near the battery along the negative battery cable. If you add electrical accessories to your vehicle, be sure to ground them to a suitable body ground such as the frame or engine block area.
------------------------------------------------------------------
So the best thing to do is to swap the wire from the battery terminal to the engine ground and as soundnsecurity said use a heavy AWG to the engine ground to the chaise and ground everything to the frame.
Also stopped off at the Nissan dealer and spoke to a few mechanic's and they confirmed, that it doesn't matter the wire type and size, only that it need to pass thru the sensor and ground to the engine block.
One mechanic even told me that he upgraded his ground and it improved his idling & cold starts, had it for a year or so and no problem with the charging system to date. ------------- The best tool in my work shop, is my BRAIN!!!!
Posted By: oldspark
Date Posted: September 28, 2012 at 12:46 AM
Deleted and reposted - it's amazing how a wet slidy drive clears the brain!
That's good research and it makes sense.
I figure that they monitor current to determine when the battery is fully charged and drop the charging voltage from the normal max of 14.4V (probably 14.2V) down to a float voltage of about 13.4V. The fully-charged acceptance current - aka float current - is up to 2A for a large 12V battery.
[ Before my sideways clarity I was curious if it was another "ECU controlled" alternator which AFAIK is only for improved acceleration but at the expense of fuel economy (in most circumstances). ]
Normal vehicle charging systems use mere voltage regulation and have no need top monitor current - ie, alternators sense the voltage and adjust rotor current to maintain it at (say) 14.2V.
It'll be interesting to see if Nissan (and others) continue with this system. It is probably to improve battery life. In theory a 12V lead-acid battery should normally be charged at 13.8V and then drop to its float voltage of ~13.4V once fully charged. In practice, in vehicles charging voltages are now typically 14.2V or a max of 14.4V (steady-state) as the older 13.8V was too low to reverse sulfation that occurs in discharged batteries - hence leading to premature failure - and few bother with float voltages. Temperature compensation is usually the only sophistication that vehicular charging systems have.
The current sensor appears to be a loop sensor as opposed to a shunt (series resistor). Hence it should not be bothered by higher currents to & from the battery (even if the cable size could be and is increased), not that changing the alternator makes much difference to what current the battery accepts, or supplies.
If the battery -ve goes direct to the engine and is left as is, cranking won't improve unless the +ve cable from the battery to the starter is improved. However improving the engine to chassis cable if the battery- goes to chassis will improve cranking.
But a heavier cable can probably be run thru the current sensor even if stripping and re-sheathing one end to thread thru, through the inner diameter of the sensor is probably plastic that can be partially removed, though I'd ensure it is still insulated from the cable, and weatherproofed.
Note too that if the higher output voltage is preferred (ie, to its 14.2V - 14.4V instead of its ~13.4V float voltage), running a load of 2A or more direct from the battery should do the trick. The current sensor will sense that "extra" load and think it's the battery's recharge current and - by never dropping to less than a few Amps - deduce that the battery is not yet fully charged and will maintain the higher voltage.
That of course assumes that the current sensing is to adjust the voltage (for/to float) as I described. If the sensing is for other reasons, let me know and I will reinvestigate.
And there are other possibilities to maintain higher voltages. One of them is to fit a normal alternator (I suggest at least a 2-wire, ie, one that has an S or Sense input).
Posted By: krush
Date Posted: September 28, 2012 at 10:05 AM
spark- my thinking was on the same line (not as in-depth to your level) the sensor is mainly to reduce idle RPM and overall RPM on daily driving to increase MPG, as Nissan trucks have a pretty good MPG for the engine size. Also to increase battery and alternator life?[in-theory]. This may also explain the rough idle, at times its like being in a paint-shaker to as smooth as a Bentley LOL.
But lets see how this plays out as Ohio Gen as shipped my new HO Alternator as of today. Should have it in a few days!!!!!
Yellow top is getting pickup on Saturday.
WAIT I JUST RECEIVED A UPS DELIVERY!!!!!!!!!!!
------------- The best tool in my work shop, is my BRAIN!!!!
Posted By: oldspark
Date Posted: September 28, 2012 at 10:44 AM
I doubt it's to reduce RPM since alternator's have little effect - even 50A is only about 1HP which shouldn't matter much. Air-cons however take a few horsepower (and hence idle increase).
Road RPM is set by gearing etc, and fuel usage is MUCH higher than at mere idle. And too low an idle increases stall risk etc.
You could be right - I have seen some (IMO) crazier ideas & implementations by OEMs - though I still think it's to drop the alternator to a float voltage. (Let me know if you find official info to support a lower idle. And by official I mean knowledgeable, not some self declared expert or (other!) forum opinion.)
I guess if the original alternator does not have an input from the ECU or other circuit, it may well be some other function - like idle speed.
Posted By: krush
Date Posted: September 28, 2012 at 11:25 AM
Just got the new Alternator in.
as a correction to my first statement it was 100AMP~125AMP @ 2000 RPM not 1000RPM.
any here are the spec and pic of the Alternator.
Spec Sheet
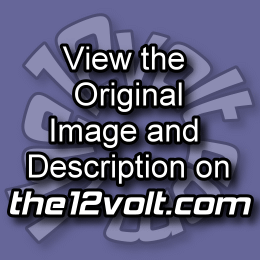 ------------- The best tool in my work shop, is my BRAIN!!!!
Posted By: oldspark
Date Posted: September 28, 2012 at 6:51 PM
Geez - it's virtually nothing (16A) at 1600RPM.
My ~90A alternator puts out at least 50A @ 600RPM ('cos I measured 45A battery charging current at idle).
But your table is alternator RPM and I'm talking engine RPM, though my RPM ratios is almost identical (a 1:1.04 pulley ratio).
You might however find lights dipping at idle...
Nice max output though.
Just make sure you don't have any faulty (collapsed cell) AGMs connected! (Nor any other "dry" or boiling battery for that matter.)
And if viewable, check your battery fluid level now & again. 14.5V is borderline high-side, especially if no temperature compensation.
PS - Whilst preparing the toast & coffee I am now devouring, I was thinking of an old school project.
The plot was someone that intended to reduce the idle speed of their V8 for improved fuel economy during peak hour traffic.
I can't recall exact figures, but the RPM drop was something like 100-150RPM and the "peak idling" time was reasonably substantial - ie 20-30 minutes per day.
The result was a $0.75c saving over one year. I remember thinking how surpisingly little it was, but idling does consume little fuel.
That 75c is now probably $2 (AUD$), but stateside it's probably 75c today (cheaper prices).
And BTW, the data we used was from lab testing.
Posted By: krush
Date Posted: September 28, 2012 at 8:05 PM
i saw that too on the low side of the chart. I hope (pray) the output is higher at engine RPM at idle. I think the yellow top should help and keep up with the alternator. Your wisdom is greatly need?
Do you think a cap would help in these install. I have a Alum-pro CAP5 that i can put in?
------------- The best tool in my work shop, is my BRAIN!!!!
Posted By: krush
Date Posted: September 28, 2012 at 8:16 PM
here are the spec on the yellowtop from there site:
Battery Model: D35
Part Number: 8040-218
Performance Data
Cold Cranking Amps: 620
Cranking Amps: 770
Nominal Voltage: 12 volts
Open Circuit Voltage (fully charged): 13.1 volts
Internal Resistance (fully charged): 0.003 ohms
Capacity: 48 Ah (C/20)
Reserve Capacity: BCI: 98 minutes (25 amp discharge, 80°F (26.7°C), to 10.5 volts cut-off)
Recommended Charging
The following charging methods are recommended to ensure a long battery life:
(Always use a voltage regulated charger with voltage limits set as described below.)
Model: D35
These batteries are designed for starting and deep cycling applications and for use in vehicles with large accessory loads..
Recommended Charging Information
Alternator: 13.65 to 15.0 volts
Battery Charger: 13.8 to 15.0 volts; 10 amps maximum; 6-12 hours approximate
Float Charge: 13.2 to 13.8 volts; 1 amp maximum (indefinite time at lower voltages)
Rapid Recharge (Constant voltage charger): Maximum voltage 15.6 volts. No current limit as long as battery temperature remains below 125°F (51.7°C). Charge until current drops below 1 amp.
Cyclic or Series String Applications::
14.7 volts. No current limit as long as battery temperature remains below 125°F (51.7°C). When current falls below 1 amp, finish with 2 amp constant current for 1 hour.
------------- The best tool in my work shop, is my BRAIN!!!!
Posted By: oldspark
Date Posted: September 29, 2012 at 9:54 PM
A battery does not "keep up" with an alternator.
The alternator either supplies the full load else the battery partially supplies the load.
A cap will have no effect. Even the smallest battery is equivalent to several thousand Farads.
And people that say a battery only supplies from below ~12.7V, or 13.1V according to those Optima specs, should investigate a battery's surface-charge "capacitance". (After recharging, a battery's open circuit voltage is usually 13.6V or higher. That can take ~24 hours to bleed off, or minutes with headlights etc.)
A battery is the best cap.
The only use for a cap is to protect AGM batteries from high-current surges (discharges, eg as found in multi-kW audio systems) when there are not enough parallel AGMs, or when voltage smoothing is required and a battery is not suitable.
I wonder how many engine bays are under 125°F (51.7°C) or how many temperature monitor their battery?
Not that Optima is the choice of many that I know.
Posted By: soundnsecurity
Date Posted: October 02, 2012 at 12:02 PM
be careful with using a yellow top as a main battery. it is more meant for using as a reserve battery so if you drain it a little it might not have the cranking amps to start your truck.
-------------
Posted By: krush
Date Posted: October 23, 2012 at 12:23 PM
I replaced the factor ground with Knukonceptz Kolossus 4-awg. It was the best wire for the money that would fit in the thought the ground sensor. The sensor opening is 13mm so what ever wire you get it cant be larger then that.
Removing the ground and sensor:
1) start by removing the ground on the battery and then the positive terminals, Put a duct tape over the positive terminal (i like to play it safe). remove the battery for better open work space.
2) remove the connector on top of the ground sensor( I used needle nose to press the clip).
Then the sensor from the metal bracket(slide it straight up... may need a little force).
3) remove the 10mm bolt connecting the middle ring terminal of the ground wire to the bracket. Last remove the bolt from the engine side of the wire.
Remove the Paint and clean surfaces:
1) remove the 10mm bolt in the middle connecting the bracket.
2) sand the front and back of the bracket and the bottom plate of the area where the bracket sits on. Also sand and clean where the wire connects to the engine( i used a wire brush)
Make the wire.
1)Start by getting whole wire length on the new 4-awg. use the old wire for measurements. stripe and solder one end with a ring terminal and use heat shrink tubing.
2)next you will need to get a ring terminal that has a splice in the barrel so you can open it up to connect it in the middle. Crimp and then solder the middle terminal don't forget to slide in a hear shrink tube before you put the terminal on.
3) Next slide the sensor back on the wire before you put on the last ring terminal or in my case I change the battery terminal that use open end wire.
4)Finally connect it all back up in reverse order and you don't.
Now you have a solid ground from your battery to engine.
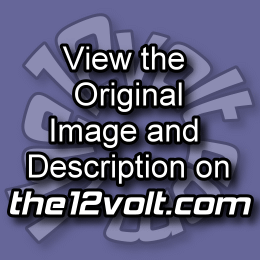 ------------- The best tool in my work shop, is my BRAIN!!!!
Posted By: krush
Date Posted: November 06, 2012 at 2:59 PM
Upgraded the cheap 12awg ground from the engine block to the frame on the drivers side with 4awg. Next will be to upgrade with a 0awg to the Engine ground where the battery is also grounded to the main frame. Also will add a 0awg at the rear where the amp rack will be for the JL Audio 1-500/1 and 2-300/4 amps to the main frame on the driver-side.
Then comes the biggie, Ohio Gen Alt install :)
 ------------- The best tool in my work shop, is my BRAIN!!!!
Posted By: krush
Date Posted: February 02, 2013 at 3:03 PM
OK just received all the power and ground wires for the Alternator and amps. I love KnuKnoceptz wires. All ready at $600 just for the power, ground and RCA cables. As soon as it warms up in here i can do my Alt and power wire install.....
1/0 main power kolossus
1/0 and 4awg kolossus
------------- The best tool in my work shop, is my BRAIN!!!!
Posted By: krush
Date Posted: February 02, 2013 at 3:21 PM
SO guys i need some help......
I want to replace the OEM battery in the pathfinder
I am looking at XS and optima yellow top brands, can anyone give me any suggestions..... oh ya, money is not a problem, i just want the best and hassle free??????
------------- The best tool in my work shop, is my BRAIN!!!!
Posted By: oldspark
Date Posted: February 02, 2013 at 5:49 PM
If you are only using one battery, then I'd stick with a wet cell rather than an AGM. They are far more robust for typical vehicle use.
Different if it's a dual battery setup.
WRT AGMs, I know nothing of the XS Power, and I have never recommended Optima in this millennium.
I have often read great things stateside about Kinetic, and after writing about my local recommendations, many agreed that Deka are also good. Alas my beloved Yuasa have apparently dropped quality and are too expensive compared to the others recommended.
But for cranking, wet cells are the more robust. And certainly if ever (over-) flattened, wet cells are the way to go. But some have excellent results with AGMs as their main battery, though AFAIK, they are still rarely as price effective.
Posted By: fuster
Date Posted: February 20, 2013 at 9:21 PM
You picked the right company for your high output alternator purchase. They are one of the only, if not the only, major maker of these units to provide a written test certification with every alternator. If they say it puts out a value at a certain rpm, it puts it out because you can see it on the test results. Tom is a great guy to talk to as well.
------------- Chronic, late stage optimist.
Posted By: soundnsecurity
Date Posted: February 21, 2013 at 7:28 AM
ive had mixed results with ohio generator. we put a 250A in a honda CRX a long time ago and the alternator didnt make it 30 minutes before it self destructed. the system in the CRX was two soundstream taraltula 2000D's on 6 T5 10's. it hit hard for about 10 minutes and then we noticed the power slowly falling and thats when we realized the alternator was dead.
-------------
Posted By: fuster
Date Posted: February 21, 2013 at 3:25 PM
If you talk to Tom about the application, he'll get you the right product.
------------- Chronic, late stage optimist.
|