Custom Electric Parking Brake Switches
Printed From: the12volt.com
Forum Name: Lights, Neon, LEDs, HIDs
Forum Discription: Under Car Lighting, Strobe Lights, Fog Lights, Headlights, HIDs, DRL, Tail Lights, Brake Lights, Dashboard Lights, WigWag, etc.
URL: https://www.the12volt.com/installbay/forum_posts.asp?tid=148192
Printed Date: August 16, 2025 at 10:28 AM
Topic: Custom Electric Parking Brake Switches
Posted By: ronemca
Subject: Custom Electric Parking Brake Switches
Date Posted: October 27, 2024 at 1:50 PM
I've been asked to figure this out, and I know from wonderful past experience with this forum that there are gentlemen on here that can do this with their eyes closed. So - I come to you hat in hand for a solution, please & thank you:
This is a custom electric parking brake installation on a snarly 4x4 retro-build. During off-road adventures, the necessity occasionally exists for just one wheel to be locked. Therefore...
The owner wants three switches;
LEFT brake on/off
RIGHT brake on/off
BOTH brakes on/off
In each case, the switch needs to be illuminated, and push-click-on/push-click-off.
The squirrelly part is this:
The mechanism does not operate like a light; it is not on-when-energized and off-when-de-energized. Rather, it operates by reversing the flow of power. I'm still getting my head around it, but as I understand it there is ALWAYS power going to the mechanism. The variable is...to which side (pole/contact) the power is being sent. I'm guessing there is no return spring or other mechanical retract function. Instead, the brake is cycled to the OFF position by reversing the flow direction of the current.
For this reason, the switches need to be wired so that they are in the "off" ("out"..."up"..."not depressed") position when the brake is OFF. This will be the usual mode for normal driving and most off-road driving.
I'm assuming that it is not possible or simple to accomplish this with fewer than three switches...but if it is - please enlighten me!
TIA!
Replies:
Posted By: lee.lopez
Date Posted: October 28, 2024 at 10:02 AM
Do you have a schematic for this mechanism or a manual? It might help to visualize better.
Posted By: ronemca
Date Posted: October 28, 2024 at 3:22 PM
That's a good thought. I'll look.
Posted By: ronemca
Date Posted: October 28, 2024 at 3:58 PM
Egad. This is what separates the men from the boys. These things make my brain hurt, but to some of you - they positively sing.
Note that the actuators will be installed...but the BCM and all that circuitry to the left will not be there. Instead, separate/dedicated circuits will be fabricated & run to the LH & RH actuators. The puzzle is - am I right to conclude that there is ALWAYS power going to the actuators? And we just need to figure out which side needs to be energized in order to activate the brake...and therefore which side needs to be energized to DE-activate the brake. I think.
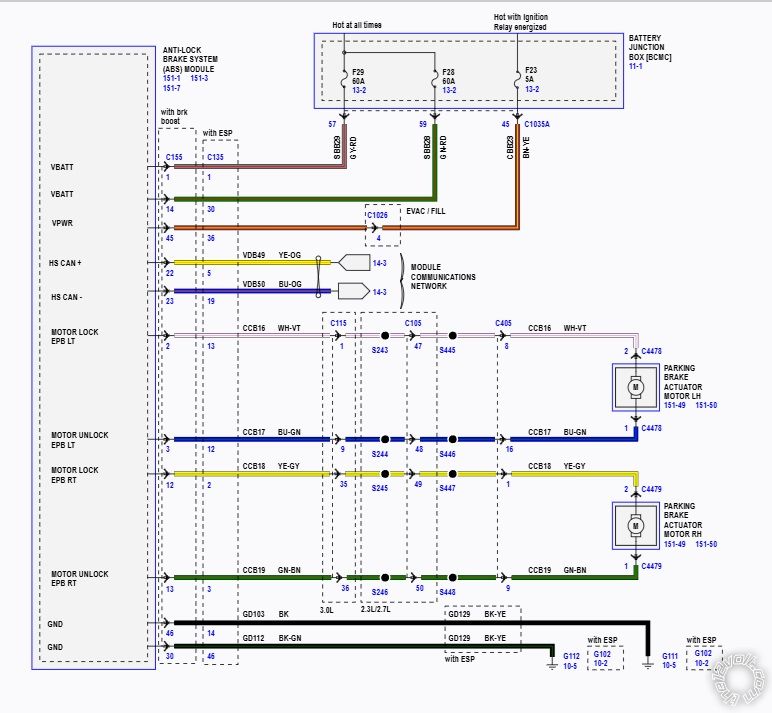
Posted By: ronemca
Date Posted: October 29, 2024 at 6:30 AM
The way it has been explained to me seems improbable. I would have expected that the mechanism has a spring of some kind that applies the parking brake when the power is off. (The DEFAULT) Then when the power becomes available once more--and the signal is sent to release the brakes--the spring releases.
But I'm being told that - no - the brake is applied by energizing one side of the actuators...and released by reversing the flow/direction (and sending power to the other side of the actuators)
<scratches pointy head>
Posted By: lee.lopez
Date Posted: October 29, 2024 at 6:56 AM
Would it be possible to wire them like reverse polarity door locks, then? Something like this for example: https://www.the12volt.com/relays/relaydiagram4.html
Or does power need to flow constantly to keep pressure applied?
Posted By: Ween
Date Posted: October 29, 2024 at 10:23 AM
https://timers.shop/Exhaust-CutOut-Controller_c_22.html?gad_source=1&gclid=Cj0KCQjwj4K5BhDYARIsAD1Ly2rXk1ky5XFoxekSKzP05ArN9r5HwVi0pXv-S23z0cQyYj6oQL9MhGAaAkxLEALw_wcB
Two of these, one for each side.
Set up for input mode 3 (latching switch). Diodes on output of 'both' switch to each controller. You'll need to adjust the operation time.
Of course, need to ask. Is the customer needing system to work at all times? ie ignition off?
Posted By: Ween
Date Posted: October 29, 2024 at 11:35 AM
Or timersshop reversing motor controller with custom firmware. Maybe contact them, they're usually quick to respond.
Posted By: ronemca
Date Posted: November 01, 2024 at 9:06 PM
Thank you for the input, gentlemen! This is still a W.I.P., and I am still awaiting some clarification on a couple of issues. Please don't abandon me - I promise to follow up when I have some relevant/helpful data!
Posted By: ronemca
Date Posted: November 09, 2024 at 9:33 PM
241109:
Okay! I initially drew up a sketch:
And then my good friend & fellow member gave me a wee tip, and I've run with it! Here's a sample of what I found:
So...I hope (and expect) to find a second matching switch (SPDT?) that will provide for the activation/de-activation of both brakes. But at least I am making progress! Thanks, the12volt!
Posted By: burntkat
Date Posted: November 10, 2024 at 7:53 AM
Very interesting project. It falls in line with stuff I am into.
I think the person giving you this info is 100 percent wrong, leading to confusion. Braking in an electric motor context is done by shorting the poles. There is no way the motor is getting current 100 percent of the time.
Although I must admit, it's been years since I was involved in fabrication of motor controllers.
A quick Google search on the tech refreshes my memory a bit and leads to a salient question - first we need to know what sort of motors we are dealing with. I ASSUME they are brushless, as brushless are more efficient. But we need to know - so, is there a commutator present on the motor? A better question would be, how many wires are present, AT the motor? 2 wires would be a brushed motor. 3 wires would be a brushless. More than that... I'll have more questions.
What did the motors come out of?
What is actually controlling the motors? Ie, you need some sort of speed controller, at the very least, unless you plan on providing full battery voltage to the motor on/off (in which case, this whole thing is a exercise in futility, as the vehicle isn't going to be controllable, nor the drive train particularly long for the earth). I ask because - whatever is controlling the motors, is also going to be doing the braking. It then leads me to the very real possibility that trying to do the braking solution in hardware, when basic braking (brakes on/off) is already being done in software, is a great way to fry the output MOSFETS, IGTs, or whatever they are using.
TLDR - need more info. Source of motors? Type/tech of motors? Controllers?
------------- "Always listen to experts. They'll tell you what can't be done, and why. Then do it. - Robert A. Heinlein"
Posted By: ronemca
Date Posted: November 10, 2024 at 1:32 PM
Each motor has 2 terminals.
Most late-model vehicles now employ electric parking brakes. On the back side of the LH & RH hub is a small box that contains a small DC motor. Assuming the brake is ON when the driver hops in the vehicle...
When it's time to move, the driver presses the [factory-installed] switch...at which time the little motor whines for...say...2.17 seconds. It spins a short shaft which retracts the pad away from the rotor...and then stops. The pads are now fully retracted from the rotor, and they will stay that way forever - until or unless the driver lifts that same switch.
When he gets to McDonalds and he's getting ready to hop out, he lifts the switch. The little motor whines for...say...2.17 seconds. Once again it spins a short shaft in the opposite direction because he lifted the switch which reverses the polarity. This squeezes the brake pads against the rotor to lock the wheel. The pads are now tightly pressing against the rotor, and they will stay that way forever - until or unless he presses the switch again.
Under "normal" conditions, the brake is now applied...the engine (and therefore the flow of power) is turned off...and the brake remains locked until power is sent--in reversed polarity--to release it.
The unknown factor is:
What controls the duration of the power? When the driver lifts or presses the momentary switch, he does not do so for a measured length of time. He simply gives it a tug/jab, and the little motor runs for a brief time and stops. And - evidently - it is always exactly the right amount to fully apply (or release) the brake.
So. We remove the circuit that came from the factory and run a new feed controlled by a DPDT Reversing Momentary switch, and we give the switch a brief tug. Does the little motor run for 2.17 seconds? I'm betting no. I'm betting it will run for as long as we maintain upward pressure on the switch...which will presumably burn out the motor fairly quickly. (Or--if we are hyper-aware--we maintain the upward pressure for...say...1.88 seconds...which may not fully apply the brake! Not good.
|