
honda 125i led bulb conversion, ac dc
Welcome Guest :)
Posted: September 10, 2014 at 1:37 AM / IP Logged



Hi the12volt!
I am the proud owner of the Vietnamese version of the Honda ANF Innova 125i. While it might not inspire bike envy in most, it treats me well and I love it to bits.
At the moment I am in the middle of converting the lighting system. I have found LED replacements for the winkers, brake/tail light, parkers, and headlight. While I understand that there may be those who dislike LED headlights, there is very little policing of laws regarding modifications here and I am convinced that the bulb will be an upgrade from the current one (single 35/35W halogen). Given that the stock can also run off DC, the argument about whether or not to try the LED headlight is moot anyway.
The stock electrical set-up for the bike is an alternator running to a regulator/rectifier where AC power then goes to headlight/parkers and DC power goes to the battery and most everything else. The entry in the shop manual states: 'SCR/ opened/single phase, half wave rectification.'
Obviously the LED headlight will require DC power, so at minimum it will be necessary to make that change to the electrical system. At this point, I wonder if it wouldn't be worth converted the whole system to DC and having the headlight run off the battery. Alternatively, I assume that I can simply not have anything drawing current from the AC connection at the regulator/rectifier and connect the headlight to the battery without converting to DC.
According to my calculations, the power saving from replacing the winkers, brake/tail light and parkers with LED bulbs is about 30W. The LED headlight will consume less power than this. Can I therefore assume that the regulator will be able to supply enough current to the system to just hook up the headlight directly to the battery (with a fuse of course) without any further modification? I have upgraded the battery to a higher Ah model than the original.
Or, would it be more prudent to go the whole hog, and convert the entire system to DC and thus utilise the full wave?
I have the wiring diagram for the bike and will happily post it, along with my idea on rewiring in the case of not converting to DC. I will post these should they be of any help.
Many thanks and appreciation for any time you can spend on my little project. :)
Posted: September 10, 2014 at 4:31 AM / IP Logged



I'm assuming the alternator is a stator or permanent-magnet rotor type. If it is a wound rotor, then full wave rectification and a typical automotive regulator is the solution.
It could be an SCR pass or dump system. For example, my old Ducati used a 2-phase SCR pass system where the SCRs were turned on to act like normal rectifier diodes. Their on time determined the average DC voltage.
Because the SCRs needed power to conduct it was not possible to push start the bike despite its permanent magnet (rotor) alternator producing power. I hence converted it to passive (diode) rectification with an SCR dumping excess power (shorting to earth) - similar to old Zener diode regulated bikes.
These days I'd probably consider full wave rectification with the same 2 "pass" diodes followed by a dc-dc converter so I don't waste any power (max alternator output was only 120W) and set the output to the usual 14.4V or 14.2V etc. (I'd probably use a buck/boost converter to get useable power even when alternator output is way less than 12V peak etc. I was using a switch arrangement that broke the centre (tap) ground and connected one output end to GND so I could double the output voltage and hence get >12V or 15V etc at low engine RPM even if at half the Amperage.)
It may be that dc-dc converters do not like raw (unfiltered rectified AC) DC voltages in which case a capacitor would be needed - the problem being it would have to be a large high-voltage capacitor with maybe a 50V rating or higher, else some disconnect system when voltages exceeded the cap voltage (eg, high RPM with negligible load).
Be wary if NOT using filtered DC. Old AC LED lighting was well known for failure because they merely used full-wave rectification of the AC and hence the LEDs saw peak voltages ~1.4 times higher than the average or RMS voltage. Newer AC LED lights use dc-dc conversion thereby overcoming that problem.
EG - an unfiltered 14.2V average (or RMS?) voltage will have a peak voltage of 20V hence probably blowing "12V automotive" LEDs which are probably rated to the common max of up to 16V. However some 12V automotive LED headlights can be used in 24V systems (ie, 28.4V typical; 30V or 32V max.
Whilst unfiltered rectification is usually not a problem in car alternators since being 3-phase their full-rectified voltage has little ripple, 2-phase systems aren't so lucky. Of course in cars etc the battery acts like a big filter capacitor, but I'm considering the raw unfiltered DC that a 2-phase (or single phase) system presents to a dc-dc converter.
I don't know if the above gives you some ideas to investigate. If your alternator typically provides a good voltage, then straight rectification into an SCR-pass or other power regulated system to the battery and other loads is fine keeping in mind that such regulators need to regulate the alternator's full output current (as opposed to typical automotive alternators where the regulator merely controls up to a few Amps to the alternator's rotor.
Keep in mind that - depending on definitions - DC does not mean "smooth". EG - half- or full-wave rectified AC is DC even if it varies from 0V to +<whatever peak>V.
FYI - whilst the voltage from a DC battery (say 12V) with a 60Hz 5V AC ripple is DC, mathematicians, circuit designers & engineers etc with treat that as "12V DC with superimposed 60Hz 5VAC". (Nobody should consider that example merely "AC". However 12V DC with 20VAC is considered by some to be AC but it is really 20VAC with a 12VDC offset, or 12VDC with 20VAC ripples etc.)
Posted: September 10, 2014 at 10:57 AM / IP Logged



Right, well, firstly, I'd like to thank you for taking your take to author a detailed reply to my post.
I will be straight up with you and say from the start that most of your response went over my head. However, I will spend some time over the coming days to endeavour to gain a fuller understanding.
In the meantime, I am not sure if the wiring digram will clear up any vague areas, such as the type of alternator. As for the LED headlight, I am not entirely sure what information, other than it has the H4 connector and a ballast.
This alternator only provides 140W by the way. I have done a few basic tests with a multimeter (voltage across battery while running, current leakage etc) and the original system seems in fairly good nick.
Here is the wiring digram: http://www.imghack.se/207295
And one I annotated with my thoughts (which seem incredibly rudimentary in the face of yours): http://www.imghack.se/207294
Thank you again.
Posted: September 10, 2014 at 8:06 PM / IP Logged



How nice to have a good wiring diagram! Maybe I should have asked for that in the first place!
Firstly ignore all I said above. Tho it still has merit, I see now that your bike has an ECM etc and that means a good DC supply - ie, good enough to run LED headlights etc.
I haven't looked thoroughly at the original circuit nor your mods, but my idea would be to move the YELLOW from the Regulator to the battery, hence the lighting gets the same DC as the ECM etc.
However that adds the LED loads to the "DC" circuit - can the Regulator handle that?
The alternator will since it's merely a single winding. (Some bikes have one winding for the "DC", and another for the headlights.)
If keeping the bulbs I'd be wary, but utilising LEDs means far less power - usually a 20:1 ratio...
But let's assume a 10:1 power/current saving... The original 35W headlight is about 3A hence its LED equivalent is ~0.3A which IMO not much and is unlikely to blow the regulator.
Furhermore, the indicators and brake lights are powered off the V01 circuit (IGN switch) which may also be "DC" as opposed to the unfiltered lighting voltage. (I'll call the latter "AC" meaning "unfiltered rough DC" even tho it is DC.)
If so, their LED conversion has lowered the peak current thru the regulator. (I'll trace the circuit more thoroughly later to see if I can determine if they are AC or DC.)
Note that converting indicators to LEDs probably means a new else modified flasher can. (If a modifiable electronic type it will almost certainly be DC powered but a "traditional" electro-mechanical (thermal) flasher could be AC or DC. I recently modified my electronic flasher can for lEDs by increasing its shunt (heavy) resistor 10-fold, ie, from a 0.1 Ohm "link" to a 1 Ohm 1W resistor.)
I was going to suggest an additional fuse for the headlights from the battery (after the main fuse), but if it's only 0.3A or even 1A then the existing 10A (secondary) fuse should handle it.
One difference will be that you must remember to turn headlights off when the engine is not running else the battery will flatten.
I expect that as OEM the headlight extinguishes when the engine stalls (tell me if NOT so!!) but if moved to battery "DC" it will stay on with IGN.
Are you game to suck it & see?
I'd suggest finding out how much a replacement Regulator/Rectifier would cost just in case. (There may be other options including repair & upgrade.)
Also if you can get a feel for how warm your fuses and Regulator currently run and compare that to post-conversion with LEDs of the DC supply. Be warned - fuses can hot enough to burn skin. Generally they should not be hot - warm is ok - but hot can indicate underrating. (Same will wiring, switches, etc.)
Note too that if the headlight LED is a bulb upgrade as opposed to an entire reflector replacement the output may be scattered or not good or illegal. (Traditional bulbs are essentially point or line sources which can be reflectored or lensed; multiple & large LEDs are not and their light is scattered in conventional lighting assemblies.)
Posted: September 11, 2014 at 8:28 AM / IP Logged



I looked at the diagrams and essentially the lights (tails, position & headlight) are powered from the Yellow wire from the Regulator/Rectifier which I assume to be unfiltered DC.
All other lights (brake, indicators, & dash) are from the battery (via the IGN switch) and hence "clean" (filtered) DC.
So as before I reckon simply reroute the Yellow wire to the Lighting Switch to the battery via the IGN switch - ie, the BLue from the IGN switch which powers the brake & indicator lights.
The brake light is specified as 18W & indicators 10W each, hence a 'peak' Wattage of 38W with brakes and indicators on.
So if the headlights & tail & position (2x 3.4W) & brake are converted to LEDs which total less than 10W, the Regulator should handle it. If you also convert the indicators to LED (and therefore probably the flasher can (Turn Signal Relay) you have extra margin - ie, brake & position & tail & headlights & two indicators total less then 38W.
I hope that makes sense - I'm in a bit of a rush.
I did search for the Reg/Rectifier and saw one for ~£45 from a Pommie site but that might not be the correct unit.
I only found the circuit for one with 3-phase (alternator coil) inputs but that had "DC" output as well as an SCR output (ie, unfiltered DC presumably for lights etc.
Posted: September 14, 2014 at 8:49 PM / IP Logged



FYI only - I happened to search SCRs for other reasons and found (not only a circuit of my Ducati GT750 voltage regulator but) mastercircuits Motorcycle Voltage-Regulator DIY.
I thought it might be of interest since it covers so much - eg, adaptation to singe & twin coil systems; how to design; and why "shorting" is used rather than opening of circuits - one of the reasons I consider the Ducati design to be stupid.
Its design notes seem pretty good. I though that might allay any fears you have of blowing your regulator - ie, you might be able to build your own, or make a fortune selling ruggedised regulators to almost anyone
(with due permissions).
It doesn't cover the rectifier diodes but they shouldn't be difficult - 15A should handle an 140W alternator (even if RMS current thru each is half that); I'd probably get 20A or 25A diodes; maybe Schottky diodes to reduce their voltage drop & dissipated power if they aren't too expensive & they handle high reverse voltages -(MBRF2060CTG??).
BTW - there are other examples on that site including single winding full-wave regulators (if you can break your ground connection).

Posted: September 20, 2014 at 1:00 AM / IP Logged



Hi Oldspark,
Thank you again for all your input. I have been busy for the last week and haven't managed to find the time to sit down to make a decent reply.
Overall, it seems like my original thoughts were along the right track and that everything is a go to start getting in to it, so thank you!
I'll go ahead and address some individual points that you made, just to clarify.
Thank you again for all of your help. I will post up some pictures of the project for sure. You will probably laugh when you see the bike that this is being done to - it's not quite a Ducati! Then again, it does come from a particularly successful lineage!
oldspark wrote:
|
oldspark wrote:
|
Posted: September 20, 2014 at 4:45 AM / IP Logged



That's the beauty of being a single phase (coil/winding) alternator - it produces ALL the power so you don't have to worry if you need both or all to provide the total power necessary. (Even tho it looks as if total power will be less than what your "original DC source" provided.)
And any efficiency loss due to the "extra" conversion of what was AC should be negligible. The only loss is the diodes which should subtract less than 1V each.
There are "2 pin" red stop/tail LED bulbs which should be compatible with your bulb socket. I think the bulb you linked requires one pin to be GND hence requiring you to rewire.
Why not get a common tail/stop LED and avoid the complications?
Otherwise a resistor could be added, but why not keep the original wiring so the original bulb can be refitted if needed?
As I recall, yes, changing the yellow wire (for the headlights) over to the "DC" regulator output is the simple solution.
Check for yourself, but as I recall, that simply transfers the headlight(s) - and maybe front clearance/position lights & tail light - from the AC (dirty DC) to the clean/battery DC side. (Tho it also makes then battery powered - not "engine running" powered.)
And since the "new" total current/Wattage for all lights is less than what that "clean DC" handled, that clean DC supply (regulator etc) should handle it.
And yes, because a wire's new current is less than its old, there is no need to upgrade it. (Unless it does have a high voltage drop and hence lower light brightness; but some high-power LEDs use current limiters instead of resistors - eg, I sampled some LED headlights and their brightness did not vary from 9V to over 16V.)
FYI - that's one beauty of cable copper and (low frequency) AC versus DC - they both carry the same amount of power (ie, RMS voltage times RMS current). It's only the insulation that needs to vary - ie, because an AC voltage peak is 1.4 times (or whatever...) its RMS or DC equivalent, its insulation needs to be 1.4 (whatever) times better or thicker. And hence how Vancouver Canada increased its under-sea electricity link capacity by changing from AC to DC which could be run at 1.4 times the AC RMS voltage. Four DC cables then carried almost the same power as its 6 cables did using AC.)
Testing battery voltage is the key to good electrics. I have oft written about battery voltages... (And as I recently wrote in bidirectional ammeter?, ammeters are useless.)
But to summarise the general rules (which may vary with some batteries - eg AGM - but generally hold for all lead-acid 6-cell (12V) batteries at ~25C (room temp))...
- the charging voltage should not exceed 14.4V long term. (Some alternators may exceed this after cranking, but your regulator would not have any such smarts or temperature compensation.)
- a full battery is ~12.6V - 12.7V (12.67V in theory) but this assumes surface charge has dissipated. (They can read 13V - 14V after charging.)
- each 0.1V down from its fully charged voltage represents ~10% discharge. (That 0.1V varies depending on the battery and is usually more like 0.12V - 0.13V, and occasionally 0.8V, but 0.1V is a simple conservative figure to work with.
- cranking batteries should not be discharged more than 20% and deep cycles no more than 50% for "best" life. (Best meaning generally adequate for typical usage.)
- hence crankers should not be lower than (say) 12.6 - 2 x 0.1 = 12.4V and deep cycles no lower than 12.6 - 0.5 = 12.1V, or usually ~11.8 - 11.9V in practice.
- charging voltages of 13.8V or less are not enough to reverse sulfation, hence "modern" charging voltages are typically 14.2V - 14.4V (unlike old days where 13.8V was the standard 12V vehicle = charging voltage).
- sulfation occurs when a battery is not full. The more discharged the battery, the faster sulfation forms. Soft sulfation is removed by charging at >13.8V. After ~ 1 week sulfates turn hard and proper battery maintenance is required to recover (some) lost capacity.
- sulfation down to a 10% or 20% discharge level is generally considered negligible.
- keep long-term unused (wet cell) batteries on float charge else recharge every 3 to 6 months. Fully charged AGMs may go for 12 months or longer before requiring a recharge. (Batteries self discharge. AGMs have a lower self discharge rate.)
The above is a potpourri of battery considerations, and they apply to healthy batteries.
Unhealthy batteries are different - they self discharge at far greater rates. And they'll overheat with normal charging voltages (assuming they still accept charge) - especially if one or more cells has collapsed.
Battery temperature is a good indication of health. Heat means a high discharge rate, or too high a charging voltage - eg, charging a 12V battery with 2 collapsed cells (hence it's an 8V battery) means overcharging which causes heat as well as gassing which can then explode.
And of course I've gotten carried away with other trivialities. That's not a deliberate attempt to confuse you - that happens naturally with any of my rambles.
Good luck, and let me know if I (we) have stuffed up.
BTW - yes, it's a Honda. Being Jap it's bound to have far superior electrics than Ducati (which like others went to Jap electrics years ago).
Being Vietnamese could make a difference, but I doubt it. I have the highest regard for them - not that I've followed their electrical nor automotive exploits.
I expected "primitive" electrics based on the primitive(??) SCR & half rectification etc - tho that could be for ruggedness and common availability - but seeing an EMS and injection... on a "cheap" bike!
(Of course EFI is cheaper to produce & comply & maintain than carburetors.)


Posted: September 26, 2014 at 11:33 PM / IP Logged



oldspark wrote:
|
Posted: September 29, 2014 at 7:26 PM / IP Logged



Noticed the other day that the REG/REC has a 6th, as yet unused, pin on it.
It wouldn't just be my luck that this could be a spare DC output? Or more likely a spare ground?
I spent a good while searching for how to test for the DC output on a REG/REC, finding I'd need a multimeter that has a function for testing voltage drop across diodes. Alas my cheapo one doesn't.




You cannot post new topics in this forum You cannot reply to topics in this forum You cannot delete your posts in this forum You cannot edit your posts in this forum You cannot create polls in this forum You cannot vote in polls in this forum |

Search the12volt.com |
Follow the12volt.com
Wednesday, August 27, 2025 • Copyright © 1999-2025 the12volt.com, All Rights Reserved • Privacy Policy & Use of Cookies

Wednesday, August 27, 2025 • Copyright © 1999-2025 the12volt.com, All Rights Reserved • Privacy Policy & Use of Cookies
Disclaimer:
*All information on this site ( the12volt.com ) is provided "as is" without any warranty of any kind, either expressed or implied, including but not limited to fitness for a particular use. Any user assumes the entire risk as to the accuracy and use of this information. Please
verify all wire colors and diagrams before applying any information.
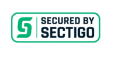