katman wrote:
I notice these units need UHF transmitters |
|
|
Only because it is a remote control which has nothing to do with this subject - I only posted that pic to show what the latching relay looked like (since there was no pic for the relay itself).
Here's a pic of it in the under/overvoltage sensor I often refer to:
( With thanks to Oatley Electronics - see
oatleyelectronics.com products_id=270 )
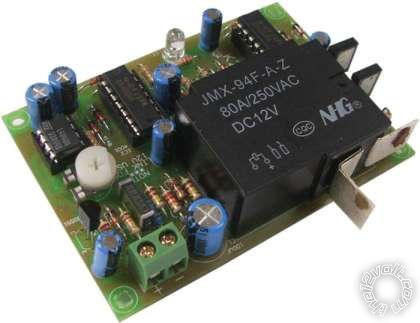
(Ha! Not only is this kit & circuit probably the best I have seen - and much cheaper than alternatives - the kit itself is almost cheaper than an 80A relay. (Ok... maybe double, but hopefully you know what I mean.) But be aware this picture is the kit AFTER you construct it, and no enclosure is included.)
You could use a push button to toggle the Oatley latching relay. I'm not sure if it would need some contact de-bounce (RC filter etc).
But, you'd have to devise some way of knowing which position it's in, and to place it in the desired state when shut off.
The Oatley under/over-voltage (aka Dual Battery) kit K227 does all that automatically and will turn the relay off if power is disconnected.
Although I initially ran the Oatley K227 up front to connect my aux battery, I later changed to the charge-lamp circuit. (In part so I could manually reconnect for jump starting; in part because I never quite finished its enclosure before pressure cleaning the engine bay. The rear "low voltage disconnect" K227 was housed in an IP65 or similar enclosure.)
This morning I posted a similar type of implementation in
using relays for auto on solutions (page 2). See if that helps.
[TIP - images with too-long filnemes will not post!]
And Jimmy is correct with his comments etc.
Remember that a vehicle's charging system is designed as a constant-voltage system to charge and maintain a battery. Hence why their settings may vary from a float voltage of 13.8V to the max long-term charging voltage of 14.4V.
Most automotive 12V equipment is rated at 13.8V (for power consumption etc) but is (or should be!!) designed to handle a reasonable time at 16V.
Exceeding 16V can cause damage. (Spikes etc may be over 200V, but they are of short duration and are a separate consideration.)
But in essence, as long as the battery gets its required voltage range (13.8 to 14.4V), and the load is within its limits, anything goes.
Hence the different techniques such as running driving lights etc direct from a higher than 14.4V alternator output whilst limiting the battery to 14.4V. (Eg, maybe dropping diodes or resistors, or the wiring & fuse losses from the alternator to the battery. In old days they used ammeters but they have now been recognised for being as useless as they were then too.)
I did mention somewhere recently of diode and variable-resistor circuits in the alternator (regulator's) sense line to boost the alternator's output voltage. (Maybe earlier in here?)
The charging voltages etc for batteries should vary with their temperature. Cars etc are usually not such a problem because batteries will be at higher temps (engine bay or boot).
But trucks & motorbikes may have exposed batteries. I'd suspect snow machines to have their batteries enclosed and close to the engine.
Fussy systems have temp sensors on their batteries and adjust the charge to suit.
Many alternators have internal temp sensors - they assume the battery is at a similar temperature. (Alternators may also have charging profiles like starting with 14.4V or higher and then dropping to 13.8 once charged.)
And of course we all know that once the battery is charged, there is no battery current flow (excluding instantaneous load changes, and the battery's normal "float current").