
oldspark battery bank w/possible solar
Home /
the12volt's Install Bay /
General Discussion / oldspark battery bank w/possible solar (
Topic Closed)

Welcome Guest :)
Posted: May 17, 2011 at 11:23 AM / IP Logged
The voltmeters were from eBay - China or Hong Kong - I'll see what I can find...
Forget building a charger, buy one - a 4-stage charger(3-stage for AGM).
And yes, battery condition can be done with a uPC. All you need is the required battery knowledge for the basic program (see BatteryFAQ etc), then add the battery size and all its relevant charge/discharge curves at different rates/loads and voltages & temperatures, compensate for else eliminate surface charge, then assign whatever values are considered to define bad or poor etc and decide what to do about it/them etc.
I'd suggest programming a EFI ECU or EMS first as that should be a good stepping stone.
IOW - IMO, forget it. Except for hobby reasons, it is not worth it - you will spend far more time programming etc than what you would ever spend manually monitoring.
Starve a battery?
If the voltage is above (say) 12.8V, you won't be discharging any battery (except for surface charge).
Below that you have a typical non-charging parallel battery situation which you may not want, so you isolate the problem else non-critical batteries.
Otherwise when charging, keep them all connected because that is the fastest way to obtain most total recharge power.
If the alternator is below its target voltage because of excessive load, then shed batteries if you have some reason for wanting some charged faster than others - eg, you want to wreck batteries faster by using a higher charge current, or your drive time or sun power is not enough to charge whatever battery enough (eg, the cranker for the next crank, or Aux#3 for the night's movie).
Float charge - when the battery's charge current reduces to whatever the manufacturer specifies as its float current (at whatever voltage, temp and after whatever charge profile (if that matters)), then it's fully charged and its voltage can be reduced to its float voltage (say 13.8V; maybe 13.2 for AGMs). That probably requires a PWM circuit if running from a charger that is supplying a higher voltage to charge other batteries. That reduces the voltage to that battery's loads.
But higher than float voltage is needed now and again to equalise the battery cells.
If the alternator can't handle the load, get a bigger alternator. (The voltmeter indicates the under-voltage in such situations.)
If the alternator is damaged due to over-current, then get a better quality alternator - eg, a purpose-built HO, not a rewound standard alternator.
Alternators should be self-limiting wrt to overloads. It should only be severe abuse that damages them (eg, my situation with nearly 60 minutes of using the starter to rotate the engine to un-bog the car whilst the aux battery powered a winch; several engine starts for short periods then back to cranking in gear... Even then the failure was because the alternator was so hot that the voltage sensing diode desoldered itself - the main diodes and windings etc were fine).
I just use my Oatley Electonics ~$25 solar regulator for my solar setup, though I am considering an MPPT (Oatley have one for ~$85).
As to float voltages etc, I used to think that 3 years from a car battery was good, but for the past decade or two I have been getting 6 years or more. That's on systems that are set to about 14.2-14.4V and do NOT seem to drop voltage even though the battery(s) should be getting hot in the engine bay. [If 25°C is max 14.4V charging with 13.8V float, then - from memory - 60°C means max ~13.0V charging (& ~12.5V float?). I do not recall seeing such voltages even when our ambient air temp is over 40°C, yet those batteries last >6 years. (They are the sole vehicle battery; flooded/wet cells; "semi sealed"; Calcium, with "Power Eye"; typically 1/4 to 1/3rd the price of similar capacity Optima AGM batteries.)]
For some reason I am reminded of distilled water in batteries. For years, using distilled water increased battery life by an average of ~3months. That was when batteries lasted probably 3 years. So a 1:12 life increment. Distilled water >$5. Battery ~$60. IE - break even. For the more typical $80 batteries, was it worth the trouble of buying and storing distilled water, and carrying it on long trips? IMO no.
As to my 6-year batteries... I opened their "semi sealed" cover after about 3 years and topped up with tap water. Maybe again a few years later.
Others go to so much more bother for little practical gain.
I think you will find the same thing for batteries. Mind you, there are people here that spend $300 to $500 for dc-dc converters so that they can "properly charge" their auxiliary batteries. However, I argue they have poor systems to start with, and they are so gullible anyhow.
I doubt that the12volt would recommend dc-dc converters to such people. the12volt would probably suggest The Big 3 instead, and then maybe a 5c diode to boost their alternator output voltage. (You can buy those diodes here off eBay, but they are mounted in an ATS/ATC fuse body and cost $35 plus $7 postage.)
(I wonder if thicker cables and a 5c diode are more reliable than a $500 40A dc-dc converter?) (That's a joke...)
Posted: May 17, 2011 at 1:35 PM / IP Logged
I understand keeping all of the batteries hooked up while charging will produce the most total recharge of the system, I'm just concerned that if there is a big difference between the starting battery and the reserve batteries that the starting battery voltage will get pulled down by helping to bring the reserves up. I see this as being a problem if I'm not able to give them enough time to recharge enough for the starting battery to have the voltage needed for the next start.
I think I know where I'm getting confused or need more clarification.
First let me ask approximately how much voltage is lost on a reserve battery when drained to half it's capacity?
When the reserve batteries are connected once the engine is running how long does it take for the voltage to recover? Does the voltage recover at roughly the same rate as the capacity?
I guess it would help me to know what the lower limits are of the reserve batteries when not fully charged, obviously they don't go to zero volts.
The way I was thinking about it was if I discharged the reserves to 50% and the voltage went from a full charge of 12.8v to 10.8v then it would take charging them back up to 75% capacity to get to about 11.8v.
So are you saying that regardless of how long the charging system is ran either engine or other means, once the reserves are disconnected then the voltage on the starting battery would be fine assuming it wasn't discharged any more than normal for starting the engine?
Assuming the starting battery was equal in capacity to one reserve battery then once they are connected to charge you would get 12.8v of the starting battery and say 10.8v of the reserves. If I remember correctly parallel calculation is 1/((1/x)+(1/y)+(1/z)...) so with 2 reserves at 10.8v you get ~3.8v ... nope something is wrong, math is right but wrong equation and logic.
Let me try and explain how my mind goes about understanding this from a basic perspective.
Starting battery and reserves are not connected...
Crank engine...
Electrons flow from ground through starter and to positive starting battery terminal - current has flowed, capacity has decreased, voltage has dropped due to the negative side becoming less negative and positive side becoming less positive ie less "pressure" across the dielectric...
Engine starts...
Alternator starts, reserve batteries join circuit - electrons flow through ground to negative battery terminals, batteries with the lowest voltage get more current (path of least resistance), as their voltage increases current decreases and distributes more equally to all batteries...
-as alternator spins it creates a rotating magnetic field pushing electrons through the ground, this can happen because the rotating field draws outer valence electrons from the neutral copper atoms on the positive sides of the batteries which make them more positive, more electrons are at the negative battery terminals and more positively charged atoms are at the positive terminal which creates even more "pull" or pressure across the battery ie voltage and "capacity"
-so long as the alternator is running it prevents current from going backwards through it like a short because of it's rectifier bridge
-when alternator is off it acts like an open circuit and minimal charge is lost
Essentially the negative terminals are like water towers, positive terminals are like lakes, water wants to flow with gravity and reach equilibrium, the alternator is like the pump that pumps water from the lake into the water tower but has a one way valve built in, distribution piping is like wiring from the battery to a device that needs power ie a washing machine needs water from the tower, the used water then returns to the lake...
So a higher charged battery when connected in parallel with a battery of lower charge and voltage will not help recharge the lesser battery from it's own capacity, it simply doesn't charge as fast as the lesser battery at first because it has a higher resistance to being charged at that point. To sum that up, the lowest charged battery will take charging priority although the lowest charged battery at any given time during charging may not always be the same battery at a different point.
This still leaves the conclusion that the starting battery will not have much ability to be recharged after starting the engine if the reserves are much lower than it. This would be a problem if the starting battery was only capable of starting the vehicle once before needing to be recharged but most batteries are capable of cranking an engine long enough to equate to starting a vehicle multiple times, my current car battery can crank the engine for probably 30+ seconds conservatively before needing to be recharged. This means that even if I can't fully recharge the starting battery between the time I get up and get to school, it will have other opportunities throughout the day such as after my exercise class when I go to the van to make breakfast and let the engine run for 20-30 min. If that isn't enough then the solar panels while I'm in class, maybe make a smaller panel dedicated to just the starting battery.
OK! Am I close? LMAO I gotta go check out another van but I think I logically reasoned my way through that to some sort of clarity, at least more than I had :) Let me know where I'm wrong or off about, that was just to try and help myself and help you see where I might be thinking about this the wrong way.
Posted: May 17, 2011 at 5:36 PM / IP Logged
I suggest downloading the BatteryFAQ html and putting it in suitable directory/folder. The you have your own excellent reference that answers most of your questions.
Not that Bill (Darden) goes into paralleling of batteries (he cleverly fobs that off to other links) and similar issues, though I reckon I know what his view are. I also probably understand all the things he covers in a single simple sentence - ie, I now the all the sub-issues being taken into account in his "simple summary lines".
Discharge voltage - I use 0.1V = 10% (as a simple but conservative estimate).
Reality is usually from 12.6 to 12.7 (theory: 12.67V) down to about 11.4V @ 25 degrees C etc.
Voltage is proportional to capacity - but remember - that is Open Circuit rested voltage - ie, the battery's internal voltage (not terminal voltage when being charged o discharged). That 11.4V to 12.7V 0% to 100% is Open Circuit rested voltage.
Yes - a higher voltage battery will charge a lesser voltage battery, or rather, a lower voltage battery will discharge a higher one.
That's usually not a problem if followed by charging except for the added inefficiency (say 30% or more) or if currents are too high.
How long to recharge? Depends on the battery and the alternator voltage (and alternator's driving/RPM profile).
Most automotive batteries probably have 90% of their LOST charge replaced within 5-10 minutes.
You can't use parallel resistance rules for batteries.
A 12.7V & 10.8V will be somewhere between those 2 voltages.
But an OC 10.8V battery is probably damaged - 100% discharged is about 11.4V; 10.8V would appear to have about -60% capacity if such logic followed.
The rest of your reasoning is good, though don't worry about electrons - after all they are not required, and they only travel at mm per second or meters per hours or whatever. Just think of "conventional current" traveling from + to - thru the circuit (load) and back thru the source. (We don't care if the current is - tp + electrons or + to - anions or positrons....)
And if the cranker battery is isolated, it won't discharge.
If connected to others when charging and that charging voltage is above (say) 12.8V, then it won't discharge.
If it does dip below 12.8V, then you could arrange a system that disconnects the cranking battery from the alternator until the other batteries are charged OR the the alternator can supply over 12.8V to ALL the batteries and loads. (But good luck. Ensure the alternator always has a battery across it (especially if also connected to sensitive loads). And I hope the reasoning for that is applicable.)
That can be one situation where a voltage sensing isolator is beneficial, but it should have user-settable voltages, and you will have the other issues that the UIBI does not have.
Read BatteryFAQ.
Posted: May 17, 2011 at 9:08 PM / IP Logged
Where is the battery FAQ? I looked in most of the different category pages listed at the top of the site and I did a search for battery FAQ...
Posted: May 17, 2011 at 9:24 PM / IP Logged
I knew there were some things that didn't add up, not all things play by logic the way I would expect.
Essentially you are saying that a fully charged cell should read 2.11v and a fully discharged cell should read 1.9v, both at 25c. So that means a difference of .21v (10%) which means for every 1% of voltage lost there is a 10% capacity loss... Your .1v = 10% theoretically leaves 20% capacity.
When cells fail do they maintain any voltage to contribute to the battery or would a battery with 1 bad cell now have a max voltage charge of 10.55? When a cell is bad does it maintain any capacity to contribute?
I'm guessing the alternator puts out a higher voltage to charge because if it were set to run at the max charged voltage of the battery it would become much more ineffective the closer the battery got to being fully charged and would never quite get there.
I'll take a look at this some more, I've been up for going on 40+hrs from condensing all of my hard drives, reformatting the computer, working on van floor plans and dealing with the van situation! By the way I ended up buying an 83 dodge extended van for $2300, now I'm trying to decide what to do with the bench seat/bed and the 2 extra captains chairs that swivel... I'm sure I'll have a use for them some day but I don't see how to incorporate them functionally. :(
Posted: May 18, 2011 at 4:15 AM / IP Logged
Although battery voltages are based on cell voltages, it's probably less confusing to stick to the "6 x cell voltage" convention here.
(I used to work in cell voltages - eg, a 1.75V end voltage (10.5V) for a UPS battery undergoing heavy discharge, and 2.40V (14.4V) max sustained charge voltage except for "boost" or equalising (2.5V or higher = >15V) etc. But that's because we didn't care if we had 2V, 6V or 12V "mono-blocks", and we typically ran 216 to 232 cells in series for 240VAC UPS systems. FYI - that 1.75 = 10.5V might recover to over 1.90V (11.4V) if given the chance, but we'd recharge ASAP to minimise battery damage, and we'd rarely go as low as 1.65V (9.9V) which was an end voltage occasionally tabulated for some batteries.)
batteryfaq.org/
Sorry - I thought I gave that earlier (too many posts; too few spare short-term brain cells).
Although you can click on that page's Car and Deep Cycle Battery Frequently Asked Questions (FAQ) 2011 (English Version), I suggest downloading the Battery.Zip further down the page and "Just create a directory for the FAQ and unzip into it...".
[ FYI - I have a shortcut called "BatteryFAQ v20110409" that points to carfaq.htm in whatever directory it unzipped to (eg - in my case: "P:\Technical&IT\Batteries&UPS\BatteryFAQ.v20110409\carfaq.htm").
That way you not only save later download bytes, but you can boot your PC and find out why your battery is too flat to connect to the internet. (Yes - that's bit of a joke - somewhat similar to "if the light bulb had never been invented, we'd be watching TV in the dark!". ]
I found batteryFAQ to be fairly good reading - nice small sections etc....
UNTIL you get to Section 9!!!
But you should learn much - like how a Specific Gravity of 1.265 is a fully charged 12V battery at 80°F/26.7°C and corresponds to an OC terminal voltage of 12.650V. (Note how SG x 10 = voltage? In THIS case!)
That last data is from the two Tables "Specific Gravity vs. Temperature... and "Open Circuit Voltage (OCV) vs. Temperature..." - ...at Various States-Of-Charge (SoC) for a Wet Low Maintenance (Sb/Ca) or Standard (Sb/Sb) Battery in Section 4 HOW DO I TEST A BATTERY? sections 4.4.1 & 4.4.2.
That 12.650V can be compared to the 12.780V listed for "for a Wet "Maintenance Free" (Ca/Ca) or VRLA (AGM or Gel Cell) Battery" as under 4.4.3.
And on it goes....
LOL!!?? Does Bill say 12.7V (12.66 rounded) is 100% FULL and 11.9V is 0% capacity? Didn't I say 12.7V & 11.4V - but that I use a "full to flat" range of 1.0V for convenience? Hmmm!
But then for AGM (Section 4.4.3), 12.78 is 100% and 11.76 is 0%, that's a 1.02V difference. Aha!
As I said... And on it goes....
[ Geez, IMO that section is good... capacity testing etc... But that whole document IMHO is fan-fracken-tastic! I do recall in the Jan 2011 version being "alarmed" at one of Bill's statements, but I recognised its (IMO) ambiguity. My alarm-bell was quenched in later section... Relief - yet again I did NOT disagree with Bill! ]
Collapsed cells: I should just send you to guru Bill Darden. (Have I mentioned his batteryFAQ document?)
But say one cell collapses, so instead of 6x2V = 12V you have 5x2V = 10V. You can't connect it to a charger because the collapsed battery's cells will have about 20% extra voltage hence gassing etc.
You cannot parallel it with other batteries.
You can probably not power 12V equipment with it.
Even if the other cells are fine and at full capacity, the collapsed cell could restrict current flow.
But who's to say the (say) 2V drop is ONE bad cell? Maybe it's two 50% cells, or three 33% cells etc?
It may involve a reverse-charged cell - ie, one cell is -1.0V compared to the others with whatever +Voltage (eg +2V or higher).
Collapsed cells probably have higher cell resistance - though it could be lower if there is a short etc.
Essentially a bad cell is a bad battery (monoblock) that must be replaced.
FYI - for 2V monoblock systems (eg, telephone exchanges with 24 series 2V monoblocks for a 48V system), just that cell could be replaced....
OR
similarly for 6V or 12V monoblocks (eg, high-power AC UPS systems), the entire monoblock could be replaced...
BUT...
In both cases you could then have troubles with the mix of new & old batteries (monoblocks). (How many TV remote controls and other things instruct you NOT to mix new & old batteries?)
[ FYI - In practice, in telephone exchanges with (say) 20-year batteries, if the battery string was (say) under 5 years old, you might replace one or a few monoblocks with exactly the SAME monoblocks (brand, type, model - if not age).
Similarly in AC UPS systems with 10-year batteries, you might replace faulty batteries with the same if that battery string is only a year or two old.
Even then, both situations carry increased risk....
Older strings would usually be replaced outright. EG - for a UPS with 10-year life designed batteries - which would be replaced after 5 years anyhow through "preventative maintenance" - if faulty cells occurred after 1 or maybe 2 years, the whole string would be replaced. Yes - all 36 x 12V or 72 x 6V or 216 x 2V monoblocks could be replaced after a mere 2 years just because of a few monoblock failures.
Not that us mere mortals require the battery reliability of telcos and AC UPS systems, but IMO the principles are the same. Mix old and new batteries or parallel non-equal batteries and you compromise reliability and overall battery life.
Have a go at Bill Darden's batteryFAQ. It should have all you need to know about batteries - or at least, common lead-acid batteries.
Not that he discusses systems - eg inter-operability, paralleling batteries etc - that's the next stage...
And please understand the impact of a battery's internal resistance (which INCREASES with lower SOC (State of Charge)) - that is why a 12V battery can be discharged at high current to (say) 10.5V despite it having 0% capacity at well over 11V. IE - internally is an "ideal battery" of (say) 11.5V but the current I through the internal resistance R causes a voltage drop of V=IR, namely 1.0V in this case (11.5V internally less 1.0V = 10.5V terminal voltage).
Hence why after disconnecting the load, the OC terminal voltage pops back to 11.5V. (Maybe not instantaneously - it is not an "ideal" resistor. And then some slower "self-recovery" can occur to increase above 11.5V.)
And hence why an OC battery of 10.5V is in serious trouble - it should never be lower than (say) 11.4V or 11.8V or 11.9V.
But maybe it had some cell collapse or reverse charge etc that was fixed with a good charge. (Maybe high current, or after equalisation.)
Topics like sulphation/sulfation cover some of that. And note the difference between soft-sulfation (fresh; reversible) and hard-sulfation (old, often not electrically reversible, but maybe additives (INOX) etc?).
BTW - if Bill & I appear to disagree, I suggest you trust Bill. But I doubt we disagree - it's probably a misinterpretation or a special case etc.
However after fully reading the Jan11 version, I modified my "don't discharge cranking batteries by more than 30%" to Bill's "no more than 20%". Those depths will vary with opinions on what "acceptable battery life" is, but I'll stick to Bills opinion. Besides, if the recommendation for Deep Cycle batteries is to limit discharge to a depth of 50% (even for so-called 80% or 100% discharge-rated batteries), I prefer 20% for crankers - 30% puts them too close to Deep Cycles.
Ain't batteries fun!
Funny thing is - in retrospect it is NOT difficult. But neither is driving a car... in any condition, anywhere, anytime....
Except whilst still learning!
I still like to keep my replies short. (LOL)
But Bill's writing is far better and more concise than mine....
Posted: May 26, 2011 at 10:31 AM / IP Logged
I found the voltmeters I referred in my top reply on this page (page 3).
Well at least I think I found the blue LED voltmeter I have mounted in my instrument cluster (instead of 2 standard warning lamps) and another in my Mum's car - although below is from a different supplier (mine was from ebay Seller User ID: i889900) - namely virtualvillage-uk-rho; search eBay for "Mini Blue Digital LED 12V Voltmeter Panel Car Voltage" (now US$15 p&p included; I bought 2 from i889900 in March 2010 for GBP 17.60).
It still works well though a dimmer would be nice.
But there are others from various sellers. I specifically wanted a small 3-digit voltmeter. (Though I also have a larger blue backlit LCD from eBay seller sg2globa - search for "Blue LCD Digital Voltage Volt Meter Voltmeter Panel 20V" (~AUD$6 with postage).
The "Lipo Voltage Indicator Voltmeter" for 12V (3.7v-22.2v) with 1 to 6 inputs is still available from seller jackywu_23 for GBP 4.30 (free postage). One pin is the common (-ve), then next is the mandatory first battery +ve, then other battery +ve's after that. Note that it auto-senses the presence of extra batteries (voltages) and cycles through, but also cycles (albeit back to itself) if only the first battery is connected (ie, not constantly on).
And I don't know how it displays if a voltage drop is -ve.
Posted: August 08, 2011 at 3:27 AM / IP Logged
Oldspark - Hey it's been a while, I finished the summer semester and have some time to work on the van again. To keep a long story short I found a place locally that sells deep cycle batteries, right now they have some T-1275's and if I remember correctly you said it would be better to use 12v batteries in series as opposed to 6v batteries in combinations of parallel and series. The 1275's actually seem to be a better deal, normally the T-105's and 145's are ~ $60 which equates to about $120 for 12v @ 225/260ah but the 1275's would end up being $120 for 300ah, ratings at 20hrs.
I haven't seen these batteries come up from these guys before but they texted me to see if I still needed batteries and I'm thinking that 3-4 of these might be a good idea, what do you think?
I'm pretty sure 2 would suffice which would give me about 5 hours of a 300w load but I'd rather buy a 3rd or a 4th now so they are from the same batch instead of finding a need for them later and having to worry about matching them. I realize they still won't be perfectly matched but I think it would be the closest I can get without buying brand new ones and checking serial numbers etc.
I also did a little research on the alternator in the van, still not sure if it has the trigger wire for the lamp but I did find out that stock it's about 70 amps and there is a 110 available from the local parts store. So my question regarding this is would I need the slightly larger alternator since that will be my only way of charging the batteries for a while? I would prefer to get the alternator for the van even without considering the batteries but I am concerned about the ability of the stock one when I add the battery bank.
I guess to put this all very simply, what are your thoughts on the 1275's in general and as considered over the 105/145's?
Do you think stepping up the alternator is a good idea until I set up alternate means of recharging the generator?
I'm still leaning towards solar panels eventually and do not want to buy a generator.
Posted: August 08, 2011 at 4:55 AM / IP Logged
Let's see - 2.3kW per day: assume 50% daylight efficiency - need 5kW of panels. That's a minimum of 5 square meters at 100% panel efficiency, ie, 20 sq meters given typical 25% efficient panels.
Assume now $3 per Watt - that's $15,000 worth of solar panels.
As to the batteries, the less number of blocks the better - especially in parallel. (IE - better going to series 6V or 2V cells if a 12V monoblock does not have the rated capacity.)
You are getting deep cycle batteries.
What level of discharge are you allowing? 80%? 50%?
Posted: August 08, 2011 at 7:39 AM / IP Logged
Wow that sure is a lot of solar panels! I doubt I'll need that much, I know I can't fit that on the roof! The max I could get on the roof would equate to about 950w of panels if I make them myself to maximize the area coverage. I don't want to cover the whole roof with them plus I don't have that much money even if I go the DIY route which is the plan. When I get to it I'll probably start with 2-4 72w panels which I figure out of an entire days worth of sunlight you could just equate that to 4-5 hours at the rated panel power so 576/720-1152/1440.
Either way recharging the batteries will have to incorporate the alternator to some extent which is why I'm curious about whether or not I would need the larger alternator.
My goal is to not discharge the batteries less than 50%, considering the 1275's are $60 each I'd rather get 4 and only discharge down to 75% on average than 50%, besides 4 batteries is the most I could realistically fit under one side of the van.
I figure there will be days that the batteries are drained more than I can recharge since some days I'm in class for most of the day and others I'm in class for just a few hours. With 4 batteries I wouldn't have to worry about draining them more than I could recharge in a single day since the average drain would only put it to 75% I could go 2 days without recharging, that's not the plan but I think you get what I mean.
At any rate what's your opinion on the alternator?



You cannot post new topics in this forum You cannot reply to topics in this forum You cannot delete your posts in this forum You cannot edit your posts in this forum You cannot create polls in this forum You cannot vote in polls in this forum |

Search the12volt.com |
Follow the12volt.com
Sunday, July 13, 2025 • Copyright © 1999-2025 the12volt.com, All Rights Reserved • Privacy Policy & Use of Cookies

Sunday, July 13, 2025 • Copyright © 1999-2025 the12volt.com, All Rights Reserved • Privacy Policy & Use of Cookies
Disclaimer:
*All information on this site ( the12volt.com ) is provided "as is" without any warranty of any kind, either expressed or implied, including but not limited to fitness for a particular use. Any user assumes the entire risk as to the accuracy and use of this information. Please
verify all wire colors and diagrams before applying any information.
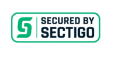