Posted: December 30, 2012 at 5:18 PM / IP Logged
Posted: December 30, 2012 at 5:20 PM / IP Logged
Posted: January 22, 2013 at 7:31 PM / IP Logged
Posted: January 22, 2013 at 9:19 PM / IP Logged
Posted: January 23, 2013 at 4:38 PM / IP Logged
Posted: January 23, 2013 at 5:03 PM / IP Logged
Posted: January 24, 2013 at 3:00 AM / IP Logged
Posted: January 24, 2013 at 5:28 AM / IP Logged
Posted: January 29, 2013 at 4:24 PM / IP Logged
Posted: January 29, 2013 at 5:45 PM / IP Logged



You cannot post new topics in this forum You cannot reply to topics in this forum You cannot delete your posts in this forum You cannot edit your posts in this forum You cannot create polls in this forum You cannot vote in polls in this forum |

Search the12volt.com |
Follow the12volt.com
Wednesday, August 20, 2025 • Copyright © 1999-2025 the12volt.com, All Rights Reserved • Privacy Policy & Use of Cookies

Wednesday, August 20, 2025 • Copyright © 1999-2025 the12volt.com, All Rights Reserved • Privacy Policy & Use of Cookies
Disclaimer:
*All information on this site ( the12volt.com ) is provided "as is" without any warranty of any kind, either expressed or implied, including but not limited to fitness for a particular use. Any user assumes the entire risk as to the accuracy and use of this information. Please
verify all wire colors and diagrams before applying any information.
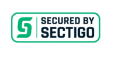