
oldspark battery bank w/possible solar
Home /
the12volt's Install Bay /
General Discussion / oldspark battery bank w/possible solar (
Topic Closed)

Welcome Guest :)
Posted: September 02, 2011 at 10:18 PM / IP Logged
Tried searching for that guy on the forums with no luck.
As far as the generator vs small motor to run an alternator the plan I was thinking of was to up grade the alternator to the 110amp instead of the 78amp like we talked about before. the C20 on each battery is 150AH so 7.5amps which I'm assuming makes 45amps for all 6. If I assume the 78 amp is adequate for the van from the factory then stepping up to the 110 means that the van really only loses 13amps (110-45=65 vs stock 78) which is a whole lot better than leaving the stock one on which would leave 33amps for the van. I don't know how much the engine and associated parts require, dash lamps etc, right now there are no interior lights, radio or additional loads other than the engine and dash lamps with one courtesy lamp under the dash on each side.
Sorry for running off there but the point I was trying to get to was if I upgrade to the 110 then that should be sufficient to run the van and charge the batteries when it's running. Instead of getting rid of the stock 78amp I could use that one to recharge the batteries when the van isn't running via the mower motor. 78amps sounds like it would provide enough headroom to account for efficiency losses etc and still deliver the C20 rate if not slightly more. So in theory does that sound like a decent idea? The other thing is compared to the 1kw Honda generator that only puts out 10amps or less at 12v it seems like a no brainer.
As far as the mounting I spent some more time trying to think of a creative way to raise and lower them with no luck. I would need a ratchet tie down that could take up about 2.5-3' which isn't going to happen. Either than or a ratcheting pulley would have the same problem which would be they would probably work ok to raise the batteries but provide no help in lowering them. I've decided that I'm just going to use one of my cheap little 2 ton hydraulic jacks with some kind of custom plate to attach to the jack cup.
With that part decided it makes mounting these things much easier which I will be using grade 8 bolts etc and unistrut. Each battery will go up individually but once they're up I will add some additional supports that connect all of them together so that if a bolt of two fails on an individual battery support it will stand a better chance of not failing completely due to the added support of the group. I'm either going to go with 1/4" or 5/16" bolts, I'm sure I could go larger but if I have 4 5/16" bolts with over 8000lb tensile strength and just under 7000lb shear strength I'm sure that would be enough per battery.
Am I correct in thinking that the most ideal location would be centered front to back and side to side with respect to the tires? I would tend to think that it would have more of an impact side to side so that should be the more important aspect and the front to back orientation wouldn't make too much difference if it was slightly more to the rear.
Posted: September 02, 2011 at 11:37 PM / IP Logged
Just thought I'd add this, I was doing some reading on using a small engine to run an alternator and they were talking about needing voltage and current regulation for recharging deep cycle batteries. Their reasoning was that without current control the batteries would try to draw the max current from the power source to achieve a minimum voltage and that only starting batteries could be appropriately governed by voltage control since they don't lose much of their charge.
With that in mind I looked at my Excel sheet I made for the different batteries I considered buying to look at how many amps it takes for the C20 and C10 rates, C20 as I said before is 7.5amps per battery for 45amp total but the C10 is roughly 13amps per battery maybe 13.5 but that equates to the 78amps of the stock alternator. The article was saying anything over the C10 causes heat and potentially distorts the plates, I'll check the Trojan website to see what they suggest for their particular batteries in terms of charge rates.
Btw the batteries I got where the 1275's if I didn't mention it which is a whopping 900AH at the C20 rate or about 560watts for 20hrs! A bit overkill but considering I'll be in the van for at least the next 2 years I said what the hell I would rather have the extra headroom and not need it then try to deal with adding more later. Plus the way I see it is it will lighten the load as a whole which would increase their lifespans, 2 extra batteries now is better than buying 4 more in a couple of years and I would really hope they last well after I'm out of the van, at least not living in it.
I'm also going to try to calculate how much I would be spending in additional gas and equipment to go the generator route either "store bought" or DIY because even just a gallon of gas a day for 2 years is a little over $2700. I've found pre-made solar panels for as low as $1.30/watt which is either slightly cheaper or right at what it would cost me to make my own. If the cost is close to what I would spend on DIY then I'd rather save my time and the possibility of screwing up my materials and just purchase pre-made ones. At most I think I would put 3 panels up there, the 170-220w ones are about 5-5.5' long and between 30-39" wide, they would go lengthwise from side to side on the van, not sure if I want to push the limits of the vans width of 76". The larger 270-290w panels are usually 77" but either way 3 panels at 220 is 660 and 3 at 290 is 870w.
Obviously that's not sufficient to really do without the generator in some form. I just checked my Excel table again and it's closer to 13.5amps for the C10 rate on a single battery, the C20 wattage at 12v is 120 and C10 is ~162w. That means a 220 panel would only need to be 54.5% efficient per it's rated power to meet the C20 of a single battery and 73.6% for the C10, for a 290w panel it's 41.4% 55.8%. So with 3 290w panels it looks like I could get at least a couple of hours between the C20 and ~C15 rate for the batteries each day baring bad weather. I'd be looking at roughly $1130-$1300 for those 3 panels so I guess the question to ask is if those panels would eliminate more than that much gas consumption.
That article on using a small engine to power an alternator said they had a 4.5hp 170cc Honda motor running a 100amp Chrysler alternator producing about 60amps for 5 hours on about 3/4 of a gallon of gas.
Anyway worst case scenario is the fridge is on 24/7 @ 8w/hr, computer 5hrs @ 300w/hr, extras 1hr @ 50w/hr, toaster oven .75hrs @ 1500w/hr, A/C 2hrs @ 500w/hr, total 343AH, ~4100WH and ~38% discharge. Realistic is fridge 24hrs @ 8w/hr, computer 3hrs @ 300w/hr, extras 4hrs @ 50w/hr for 107AH, 1300WH and 12.5% discharge. I think in the realistic scenario the 870w of panels could handle recharging 1300WH in a typical day, that's 1.5hrs of rated power from them which seems plausible, I think the most I could expect from the panels is a few hours of rated output per day so 2600-3500WH. To be honest that actually seems like the panels might be capable of handling my electrical needs, I wouldn't be running the toaster or A/C every day so on the occasion that I do then the batteries would get recharged over the next day or so.
You have convinced me of the generator even if it is just as a back up and I know you're big point was the cost of solar etc but if I could get panels in the $1.30-$1.50/w range then it seems like a viable option assuming I have the money to do so up front. I will most likely go with a generator first since the initial cost would be lower and capable of meeting my needs but in the long run I think the solar would be cheaper so long as I get it sooner than later.
Posted: September 04, 2011 at 12:02 AM / IP Logged
I just googled "Aussie50 EdSystems" and came up with heaps of links... Maybe http://www.google.com.au is better than http://www.google.com?
I don't know why you would want the additional petrol alternator when running the van (assuming you mean running its engine).
For solar, I'd estimate a typical "average" output expectancy is a max of about 200W per square meter (of panel) assuming reasonable sun and panel orientation. You then factor in your latitude & sun-hours per day.
For battery mounting, I was assuming a jack or strong girlfriend. A leverage or lowering system would add complication. Maybe a spare-wheel lowering chain setup (wheels are light though the mechanisms I have seen seem robust) else a winch. Both add volume etc, though the winch could be off-side with an overhead pulley. But winches ain't cheap either.
But even with my intended semi-sealed flooded cell (not AGM), I don't see the need to inspect that often. (Maybe after the first year depending on cycle-depth & ground surface temperatures.)
Charge-rate: As I wrote earlier, the lower the better. (Except for occasional maintenance or after a deep discharge.)
Hence ideally charged at the rate sufficient for full recharge during the charging period. And not exceeding the battery recommendations.
Hence the problem when having an adequate AH replacement charge, but over a short period (ie, higher current than over a longer period).
Having said that, cranking batteries may often take more than their recommended max 10% or 20% of C20 etc, yet they can (or will) last years longer than their warranty period.
But they are usually flooded/wet batteries which have about twice the internal resistance of AGMs (hence accept about 1/2 the charge current of equivalent and similarly discharged AGMs).
And wets are more tolerant of overcharge as they dissipate heat better (boil off electrolyte etc), though AGMs can usually accept higher currents according to specs (without damage) - as opposed to simply accepting higher currents due to their lower ESR - ie, the difference between an AGM being able to supply higher currents than wets, as opposed to them liking that higher supply - ie, without damage (that's something many car- & audio-forummers don't seem to understand!).
But that's the "Art" aspect of batteries. ("Batteries are more of an art than a science" to quote a popular "expert" statement.)
My cranking 38AH AGM - which should be quite unsuited to cranking! - takes 45A when the vehicle starts charging. That is well in excess of any "20%" C20 charging recommendation! However that AGM is still working fine after ~1-2 years in my case (and ~3 years in my brother's case).
I should add that that 40-45A initial charge drops to under 10A within 30-60 seconds, and those AGMs are a 10-year design UPS battery that were discarded after 5 years (typical for UPS preventative maintenance) and they are now ~11 years old.
Battery life and suitability is a combination of so many factors. Peak demand and recharge currents may be easy to quantify, but the effects of how long until recharge; how often the demands and recharges, ambient and mono-block temperatures etc are difficult to factor in.
And then their specs - they are often written to cover (say) 97%-99% of "that" model battery for warranty purposes - ie, they describe minimum operational requirements. Some manufacturers might stretch those specs for greater sales, whilst others know they will wiz it in. (And I know many users have a hard time making warranty claims with some batteries, whilst other manufacturers replace batteries even when they know the user is at fault.)
Posted: September 14, 2011 at 10:16 PM / IP Logged
FYI - I just saw some Honda portable inverter-type generators (no idea of the price though).
The largest was model 20 or 2.0 or similar. It was rated at 1.6kVA (so I'd assume at least 1.3kW) with a peak of 2.6kVA. It's DC output was 12V @ 8A (96W).
IMO it was ok to lift & carry.
It also had a synchronising input for paralleling with other similar types (Hondas I'd presume - unless there is a Standard).
Posted: September 14, 2011 at 11:05 PM / IP Logged
I'm actually looking into piecing together my own generator. I'm tracking down a horizontal shaft motor in the 3-5hp range with the intention of using it to run an alternator like we talked about. I think I mentioned it before, an article I read about doing this talked about the danger of not charging the batteries properly because the alternators are voltage controlled and not current controlled. With the discharge that these batteries will see, the alternator will try to bring the voltage up which when considering how discharged they are, will push way more current than they should be exposed to. According to the article and probably from our conversation here, the batteries should not be recharged at a rate higher than the C10 rate, preferably the C20. So the cool thing is that with these 6 batteries, the C20 for them will be 45amps which means if I get the right sized alternator then I shouldn't have to worry about current control so long as the alternator max output is not greater than the C10 rate.
Anyway the other reason I'm looking into this is because as you noted, those generators are only outputting about 10amps or less into 12v which is about what I need per battery. Plus I'm going to try and mount it to the underside of the van and use an electric motor to pull the recoil starter since getting a motor with electronic start capability is expensive. I do appreciate the suggestions but so far the 12v current output seems to be a deterrent for this application, correct me if I'm wrong, it just seems inadequate.
Posted: September 15, 2011 at 1:56 AM / IP Logged
Don't worry about current limiting. As per Trojan's TRJN0109_TRJNUsersGuide.pdf, they are typically charged at 14.7V or and higher, and I see no mention of current limiting. (Note that they limit themselves due to their internal resistance, especially being wet cells.)
As I often write, in general, batteries are charged with a constant voltage charger. (Some switch to a lower float voltage once they are fully charged. Some go higher than the normal 14.4V for maintenance.)
Hence use the same as your vehicle's alternator. (Then you have a spare.)
Posted: September 19, 2011 at 6:25 AM / IP Logged
Hey I was thinking about a battery charging circuit and I wanted to see if you could point me in the right direction. Again this is a DIY project. Anyway I wanted to know if there is an inexpensive sensor for measuring the specific gravity. I don't think I will be able to take individual voltage and current measurements from each cell in the T-1275 batteries. The plan is to create a circuit to monitor and record the voltage, current and temperature of each battery, preferably each cell but like I said, I don't think I can reasonably. With that I could calculate the power output, correct for the temperature and the rate of discharge to get a decent idea of how much charge the battery has lost. I can also use this to derive the Peukert (spelling?) number associated with my batteries and compare it to what it should have been when they were brand new to see how much they have degraded.
I'm also wondering if the specific gravity is related to how degraded the batteries are or if it is just an accurate way of measuring the state of charge.
At any rate since all of the batteries will be connected in parallel I would like to eventually have each line to the battery controlled by this circuit so that it can charge each battery based on it's individual needs instead of being based on the characteristics of the bank as a whole.
So pretty much specific gravity is my concern but feel free to correct me if I'm wrong about it being important. I did read that if you have active monitoring like I described for the voltage, current and temp, that it is also very accurate; gave me the impression that either that or specific gravity would be sufficient and that having both ways would be overkill.
Posted: September 19, 2011 at 8:10 AM / IP Logged
In a nutshell, I'd say forget it. No point. And certainly not SG readings.
I can say that battery monitoring requires at least 10-bit sampling for voltage. How that ties in with current, temperature, duty cycle etc for each individual battery is a different kettle of prawns altogether.
The only other thing I'll say is that wouldn't you think that after $millions spent on battery research, someone should have come up with that already?
Furthermore, let's assume my RRP $670 battery - say $500 each => $18,000 worth of batteries for a single string in a 240VAC UPS (36 x 12V) - so let's assume $10,000 worth of 10-year design batteries. Despite monitoring, they chose to replace the batteries every 5 years - that's $20k instead of $10k per 10 year cycle.
Wouldn't a "monitor" costing up to $5k or $10k be worthwhile if that could avoid unnecessary battery replacement?
And that's only a small UPS (~25kVA) - you should see the battery cost for the bigger units (up to 900kVA).
The above is a reverse way of saying that if accurate battery condition monitoring could be done, it would be.
AFAIK, not much has changed. The only way of measuring actual battery capacity is a discharge test.
And there is no guarantee that they will have that capacity or totally fail the next test or next time they are required.
The simple OC rested terminal voltage measurement is still the best cost effective test of battery condition, but that should not be confused with battery capacity - that cannot be measured except thru a discharge. (ac signal-injector testing excluded.)
Hence you merely need current and voltage (and temperature) monitoring for each battery, though as a power output figure that is useless.
Instead you would match the voltage against the expected voltage for whatever discharge rate (current or power) at that temperature - whether from battery tables or your previous datalogging.
Forget Peukert - just replace at whatever capacity you desire, the general ROT is 80%. I retired my last cranking batteries after they reached an estimated 10% (if not lower).
Posted: September 19, 2011 at 1:13 PM / IP Logged
I figured the specific gravity thing would be more work than it's worth, in theory it seems possible but the generic pressure sensors I found were about $30 each or more which makes for about $1100 in sensors to monitor all cells in my bank.
As for whether or not accurate battery monitoring is being done, well I got the idea from actual products that you can buy, those were the ones that suggested that using the power output and it's corresponding efficiency at that output would be just as accurate as the specific gravity. Take for example the digital hydrometers that cost a couple thousand compared to the cheap $30 testers, the only real difference is the development of the electronics and the product itself.
Either way it's not something that will happen right now but it is going on my list of projects to work on, after all it would be good experience for my electrical engineering degree even if in the end it doesn't work out, at least I'll know how to take it from idea to product, test it, improve it etc.
Posted: September 19, 2011 at 7:46 PM / IP Logged
I see hydrometers as a physical thing, but even then I think it is a bit oldskool. It's good to hear that you think voltage etc is "as good" - that was my opinion years ago. (And it seems I'm still relevant or up to data LOL.)
They were used on 2V cells that were the size of 2-drawer filing cabinets, but even then it assumed proper mixing of the electrolyte and that is equivalent to waiting for surface-charge dissipation for electrical measurements (surface charge being largely due to uneven electrolyte or charge distribution).
Besides which - you develop all this hydrometer stuff only to replace with AGM batteries. (Dare I mention a dork that suggested a hydrometer for someone's AGM?)
But bottom line - too expensive ELSE too complex and too much work for little gain. That may change if batteries becomes a science rather than an art....
And battery replacement tends to be a case of "can I still use it" rather than what condition it is in. EG - running a 10% capacity 40AH in my vehicle was fine with its reliable starting AND the spare ten-percenter in the back. Different if my charging source was limited solar power - then I would probably want a better battery - ie, normal ~30% cycle inefficiency - rather than whatever inefficiency my 10%ers had.
Until then, you get a good feeling for when your battery capacity is dropping. You then investigate - is it a added load or drain, reduced charging, or a monoblock in a string or bank (bank here implying parallel monoblocks or strings).
In your case, occasional capacity testing (6 monthly?) would be a known load using one string (maybe whilst the other is solar charging) and measuring voltage with time, and checking each battery (monoblock) has matching voltages.
And you don't need to know the specs of the load or battery - just compare to previous etc.
But with experience comes the desire - or not - for all beforementioned monitoring. You might know and understand all the theory (as per batteryfaq.org - download the FAQ zip every few months...) and yet the reality can be different.
My cranking battery for instance - a 38AH AGM which despite being for high discharge rate UPS use (ie, C15-minutes or C10-minutes), I would not advise for cranking. My bother reckoned he has been cranking his now 4 years, and it's still going strong. (It shows how I tend to err on the safe side, but it also shows how such advice can miss out on paradise. But that's the risk side - no risk, no gain.)
Another example being the no more than 10% or 20% of C20 recharge current, yet that is broken all the time with cranking batteries (in most vehicles).
Hence another of my commons: Suck It And See.
And you have been sucking (so to speak!). You have sucked some proposals; I have countered some. But soon you will hit the reality, and then after the law suits, I too will have gained (or lost ha ha) from your experience.
In the mean time, I/we are trying to prevent the money wastage and get the best system to meet your requirements. (Noting that batteries are not a long-term high-power source - they are still only short-term emergency (until the diesel backup genny kicks in or the AC mains returns) or a low power source for longer.
BTW - I was rapt on Saturday morning when I found a dumped washing machine (Fisher & Paykel 2005 7.5kg). I did my environmental cleanup thing and hope now to have a motor suitable for a wind turbine (~300W?). I'll let you know next millennium by which time I might have progressed...
Reminds me - I though of the difference between inverter supplies and traditional - ie, an inverter system is an SMPS where AC is converted to DC, and that DC is inverted to AC or DC. EG - those "peak power" solar chargers convert from the solar panel's "peak power" DC voltage to whatever DC voltage is required. Inverters are the way to go, but short-term, ordinary alternators etc probably the necessary starting point. (Sorry - that's vague and somewhat a sweeping statement/subject...)
It seems we both have that "now now but later" ...er, problem.



You cannot post new topics in this forum You cannot reply to topics in this forum You cannot delete your posts in this forum You cannot edit your posts in this forum You cannot create polls in this forum You cannot vote in polls in this forum |

Search the12volt.com |
Follow the12volt.com
Wednesday, August 20, 2025 • Copyright © 1999-2025 the12volt.com, All Rights Reserved • Privacy Policy & Use of Cookies

Wednesday, August 20, 2025 • Copyright © 1999-2025 the12volt.com, All Rights Reserved • Privacy Policy & Use of Cookies
Disclaimer:
*All information on this site ( the12volt.com ) is provided "as is" without any warranty of any kind, either expressed or implied, including but not limited to fitness for a particular use. Any user assumes the entire risk as to the accuracy and use of this information. Please
verify all wire colors and diagrams before applying any information.
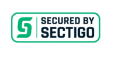