Posted: October 18, 2007 at 4:22 PM / IP Logged
Posted: October 18, 2007 at 4:36 PM / IP Logged
Posted: October 21, 2007 at 9:26 AM / IP Logged
Posted: October 21, 2007 at 11:46 AM / IP Logged
Posted: October 21, 2007 at 1:21 PM / IP Logged
Posted: October 21, 2007 at 2:42 PM / IP Logged
Posted: October 21, 2007 at 2:51 PM / IP Logged
Posted: October 21, 2007 at 2:53 PM / IP Logged
Posted: October 21, 2007 at 3:16 PM / IP Logged
Posted: October 21, 2007 at 3:22 PM / IP Logged



You cannot post new topics in this forum You cannot reply to topics in this forum You cannot delete your posts in this forum You cannot edit your posts in this forum You cannot create polls in this forum You cannot vote in polls in this forum |

Search the12volt.com |
Follow the12volt.com
Friday, August 29, 2025 • Copyright © 1999-2025 the12volt.com, All Rights Reserved • Privacy Policy & Use of Cookies

Friday, August 29, 2025 • Copyright © 1999-2025 the12volt.com, All Rights Reserved • Privacy Policy & Use of Cookies
Disclaimer:
*All information on this site ( the12volt.com ) is provided "as is" without any warranty of any kind, either expressed or implied, including but not limited to fitness for a particular use. Any user assumes the entire risk as to the accuracy and use of this information. Please
verify all wire colors and diagrams before applying any information.
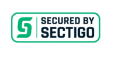